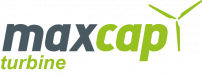
maxcap 141 is a technologically advanced Multi-MW Wind Turbine Generator (WTG).
maxcap 141 is defined by a very high Capacity Factor.
maxcap 141 achieves a high number of Full Load Hours even at locations with low average annual Wind Speeds (< 6.5 m/s).
maxcap - Unique Selling Points (USPs)
Base-load optimisation - Means more stable Power Production
The maxcap wind turbine generator is optimised for base-load operation.
The combination of a relatively large rotor with a cost-optimised generator from the 2.5 MW class is unique.
As a result, the maxcap turbine generator reaches its nominal power even at low wind speeds of around 7.5 m/s.
More frequently achieved nominal power means less volatility and thus guarantees more even power production.
This protects the grid infrastructure and favours hydrogen production, seawater desalination and the use of battery storage!
The Capacity Effect - Increases the ROI
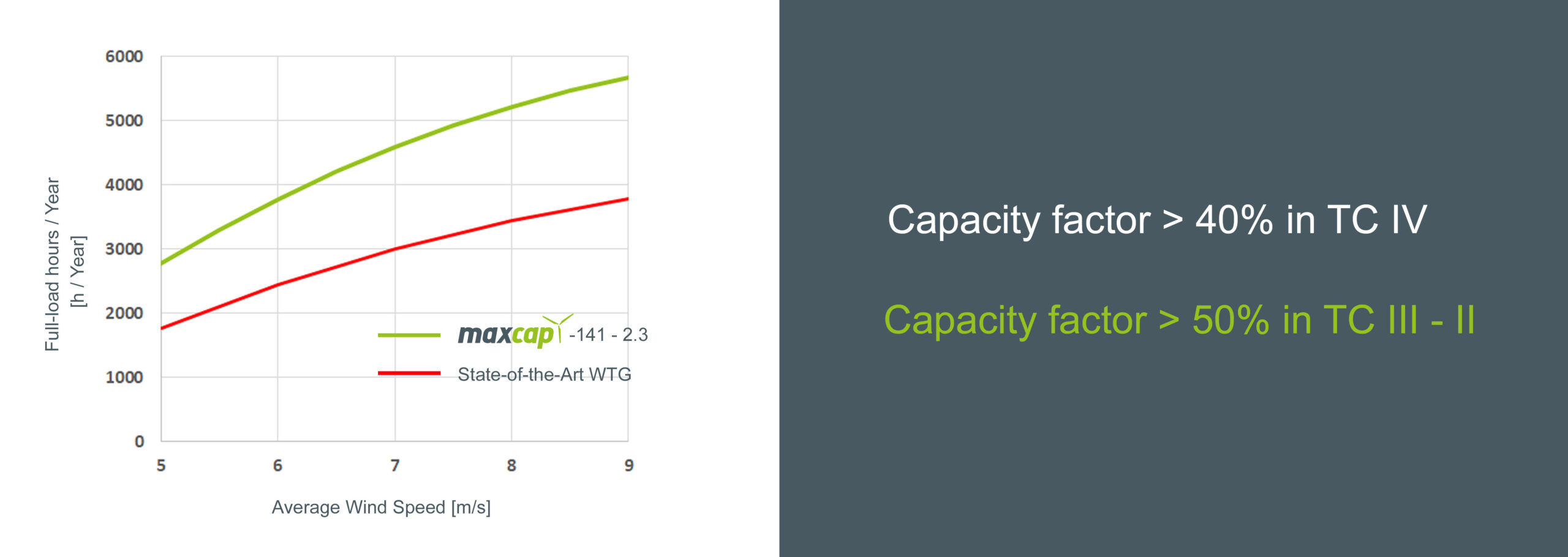
Compared to conventional wind turbine generators, the maxcap WTG achieves up to 45% more full-load-hours - the capacity of the maxcap is utilised significantly more.
Comparatively low investment costs and increased capacity utilisation have a positive effect on the ROI (return on investment).
The Balancing Effect - Lower Volatility
By reaching the nominal power at low wind speeds, the fluctuation of energy production is reduced.
With correspondingly balanced volatility in electricity feed-in, project costs for grid expansion, reserve capacities or energy storage capacities can be significantly reduced.
More accurate Forecasts for Power Production - Increases Planning Reliability
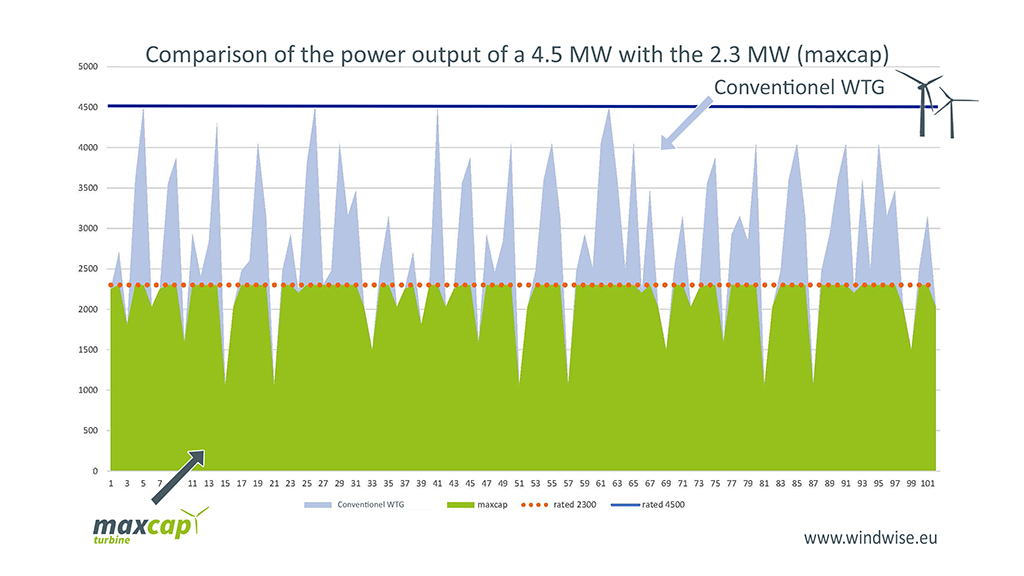
The reduced volatility of the maxcap WTG's power production increases the forecast accuracy for the expected energy production.
This means that the energy produced can be marketed much better on intraday, spot and balancing energy markets.
For investors planning security increases due to the reduced fluctuation, especially in years with little wind.
Reduced Structural Loads - Longer Lifetime
The early speed reduction of the maxcap wind turbine at low wind speeds also reduces the structural load on the turbine.
As soon as the maxcap WTG reaches its nominal wind speed, the rotor blades are turned towards the vane position via the pitch system. This reduces the thrust on the blades and on the tower.
When comparing a maxcap wind turbine generator with a conventionally designed wind turbine generator, this operating point is reached at significantly lower wind speeds. Thus, the dimensioning load level of the maxcap WTG is significantly lower than that of a conventional wind turbine.
These lower structural loads on the maxcap wind turbines correlate with the increase in the expected lifetime of the maxcap WTG.
Distance Optimisation - Expanded Chances of obtaining Building Permits
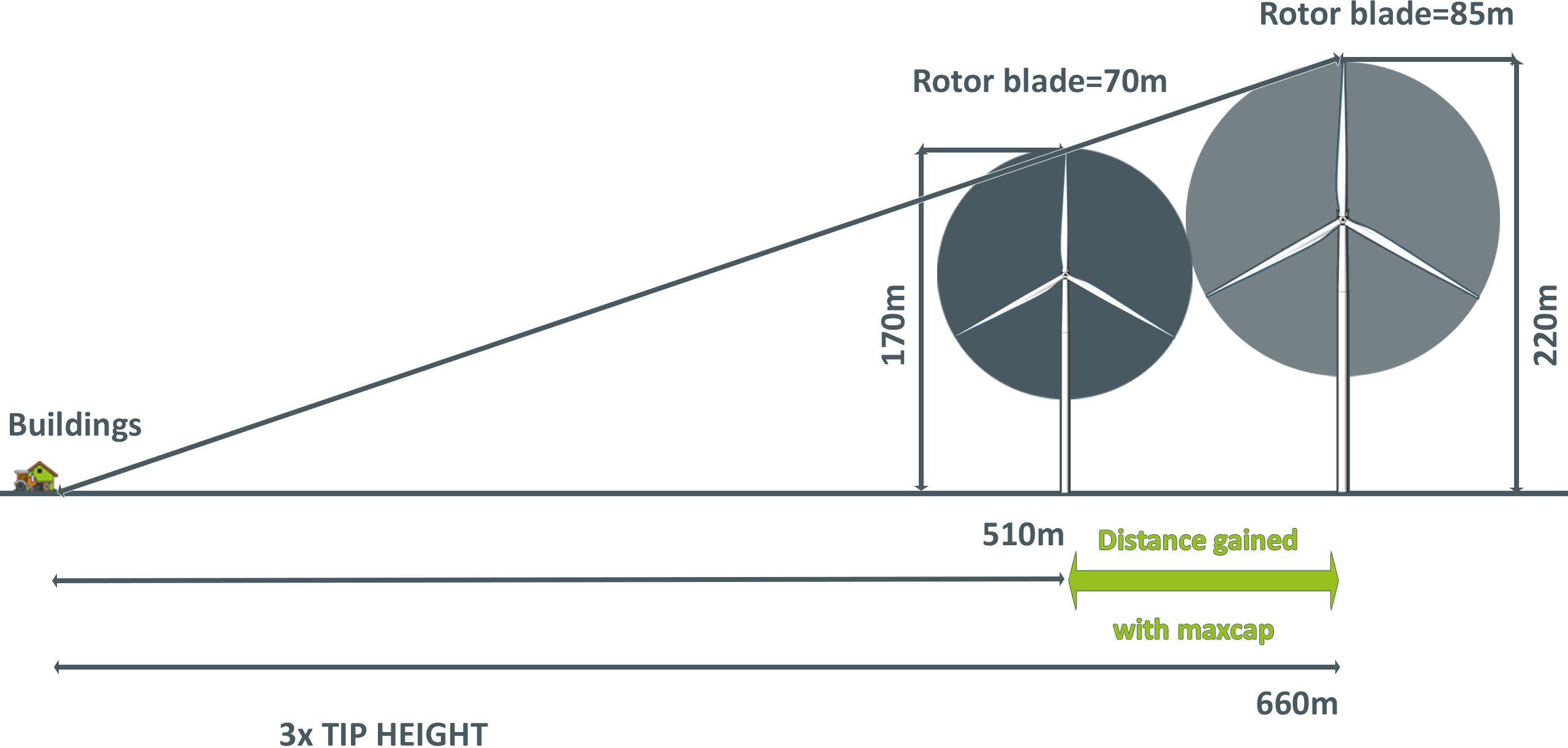
With a total height of <170m, the maxcap WTG can be realised at many locations where larger Multi-MW WTGs often cannot be installed due to the criteria of "visually oppressive effect".
This criteria usually requires a minimum distance of 2.5 to 3-times of the total height.
The maxcap WTG is a base-load optimised low wind turbine generator that can also be built on locations with limited space or close to buildings.
Decentralised Installation - Short Transmission Paths
The overall height of the maxcap allows it to be built in close distance to the consumers. This favours the effective use of the generated energy.
With short transmission paths for electrical energy, energy losses are minimised and no grid infrastructure is needed.
Self-supply becomes extremely economical. The maxcap technology not only ensures the company's own energy supply, but also significantly reduces production costs, especially for energy-intensive companies.
Improved Wind Farm Efficiency - Increases the Total "Energy Harvest"
The function of a WTG is to convert the kinetic energy of the wind into electrical energy. Logically, this involves extracting energy from the wind.
WTGs in the second row of a wind farm are in the "wind shadow", the so-called wake of the WTGs in the first row.
In larger wind farms, the so-called wind farm efficiency factor leads to a significant reduction in power compared to the nominal value of the wind turbine generators. Early shutdown not only reduces the structural loads on the WTGs, but also the so-called thrust and thus the proportion of power extracted from the wind.
WTG in the wake of a WTG, which shut down at an early stage (maxcap technology), can thus harvest more energy.
Wind farm efficiencies can be improved in this way up to 3% depending on the area.
Reduced Noise Emissions - Various Operating Modes Possible
The lower speed of the maxcap leads to a lower rotor blade speed. As a result, the noise emissions of the maxcap wind turbine generator are reduced.
In combination with so-called serrations at the rotor blade tip, the noise emission can be significantly reduced.
These serrations have basically no influence on the power or thrust curve of the WTG.
The noise emission during normal operation of the maxcap wind turbine generator is < 104 dB(A).
When designing maxcap WTGs, there are additional operating modes in which the noise emission can be further reduced. These can be selected specifically for the location and time of day.
Optimised Electrical Concept - Increased Efficiency
The power of the maxcap WTG is adapted to the frequency and voltage requirements of the electrical grid via a full power conversion.
The "grid side" of the power inverter is equipped with IGBT semiconductors. With optimised control, this enables the compliance with a wide range of grid regulations.
The generator is designed as an electrically synchronised machine. This is controlled via a so-called exciter machine, which is why the converter on the generator side can be implemented as a passive diode rectifier and does not need to take over any control tasks. These diode components are considerably more robust than IGBT semiconductors and improve the total electrical efficiency of the converter by about 1%.
IPS - Individual Power Supply - Enables Autonomy
The modular conception of the inverter system allows a control system that is capable of generating sufficient energy for the wind turbine's own self-supply even at low wind speeds or in spin mode. In this way, grid failures can be bridged and the WTG can be brought back to the grid within seconds. This functionality is called IPS (Individual Power Supply).
In addition, the braking resistors in the DC link of the inverter improve the operation of the maxcap wind turbine generators. They support the necessary individual control in weak grids.
These functionalities together recommend the maxcap turbine as an optimal energy producer not only for an electrolyser for hydrogen production, but also for electricity feed-in into a seawater desalination system for the production of drinking water.
The IPS and the braking resistors with the grid-forming capacity of the grid-side converter guarantees that the maxcap WTG can be operated autonomously in the stand-alone grid, i.e. at least for a while.
Robust Cooling Concept - Safety is Important!
The cooling concept is very robust and water-based.
A master pump controls the water cooling for the gearbox, generator, inverter and transformer in combination with a passive roof cooler and a powerful water heater for any cold-start situations.
The water circuit also provides oil cooling and thus lubrication of the main gearbox via a plate heat exchanger.
The generator is cooled via a shell cooling system with internal air circulation. The power-carrying elements of the inverter are mounted on corresponding water-circulated heat sinks.
The closed trafo unit is cooled by an air-water heat exchanger.
The power-conducting inverter systems are constructed in a dust-proof and splash-proof design. The integration of an air-to-air heat exchanger prevents the ingress of dust, liquid or other corrosive particles. An installed drying system prevents the formation of condensate in the cabinet and removes moisture.
Eine gute und ununterbrochene Kühlung der kritischen Bauteile in einer WEA minimiert das Risiko beim Thema “Überhitzung”. Mit der maxcap-Technologie setzt windwise auf erhöhte Sicherheitsstandards, die für den Schutz von Mensch und Material unverzichtbar sein sollten.
Established Suppliers - for Extremely High Quality Demands
Especially for sensitive components, the windwise engineers rely on quality and reliability from established suppliers. The selection of the components and also the suppliers was very carefully considered. Essentially, the maxcap WTG uses tried and tested systems from established suppliers that have been used in large quantities in the wind industry for years.
In times of supply bottlenecks and resource shortages, aspects such as quality, reliability and, above all, availability are becoming increasingly important.
With the support of our suppliers, we can help strengthen local markets and produce key technologies in our own country.
Proven Drive Train Technology - Compact and Powerful
Twenty years or 175 000 hours of operation under turbulent environmental conditions and highly dynamic, irregular loads: These are the requirements that must be met by the components of the drive train of a wind turbine generator.
Die maxcap-Technologie verfolgt bei der Auslegung des maxcap-Triebstranges in der Antriebstechnik bewährten Ansatz “Getriebe kombiniert mit einem Generator”.
The gearbox of the maxcap WTG is designed as a two-stage planetary gearbox. The planet carrier of the first stage is firmly clamped to the main shaft via a shrink disc.
The generator is directly attached to the gearbox.
The power is converted by a medium-speed, electrically excited synchronous generator and a full conversion system.
The full conversion system consists of a diode rectifier unit on the generator side and a fully controllable IGBT conversion on the grid side.
The transformer is located in the back of the nacelle.
The rotor bearing consists of a main shaft and two independent bearings:
- a tapered roller bearing that takes up thrust and radial load, and
- a loose bearing that absorbs the resulting radial load component.
Operators of wind turbine generators are very interested in low turbine costs, high efficiencies and minimal maintenance costs. Proven and advanced power transmission technology, such as that used in the maxcap WTG, can meet these demands.
Steel - Instead of Cost-Intensive Concrete Towers
The hub heights of 107m and 126m offered as standard for maxcap wind turbine generators can be adapted to match the specific location.
The maxcap WTG towers are constructed as cost-effective conventional tubular steel towers with a maximum diameter of 4.4 m.
This leads to significant investment savings, especially compared to systems in hybrid construction with concrete bases or pure concrete towers.
Save Energy - Reduce grey Energy
One thing is certain: Concrete and the cement it contains are particularly energy-intensive in their production and release a huge amount of emissions during production. The cement industry alone is responsible for eight percent of global greenhouse gas emissions.
Therefore, the call by climate protectionists to reduce grey energy and grey emissions is only logical.
The steel tubular tower of the maxcap wind turbine generator ensures the absolutely necessary stability of the turbine, but is comparatively less energy-intensive to manufacture than the alternative of a concrete tower.
Sustainability - Also in the Dismantling Process
At the end of the lifetime of a maxcap wind turbine, it is time to dismantle it.
With the principle of "recycling before disposal", the maxcap concept supports strategic climate protection.
The tubular steel tower in particular is suitable for recycling residual materials. Steel can be melted down, while a concrete tower only needs to be demolished and disposed of.
For an investor, there will be a positive side effect from the potential return for the steel scrap.
WINDWISE GMBH
Augustastraße 47/49a
48153 Münster
E-mail: info@windwise.eu
Phone: +49.251.590 667 0
EVERYTHING AT A GLANCE